-
Pegasus CorporatePegasus Corporate is an integrated Business Management system that uses the best practices in the market
through modern management concepts. It has purchasing processes; storage and distribution of goods,
providing agile administration, with accurate and instant information, leading to improved customer service;
well-defined internal process flow; greater control of the companys assets and liabilities and better use
of human resources. Built on the .NET platform, it operates in multi-tiers with Firebird,
SQL Server or Oracle databases. It has the possibility of remote access via Terminal Server. It is multi-company, that is,
it is able to control corporation and branches; issues electronic invoices; Sintegra; Sped Fiscal; Sped Accounting; Fcont; Sped PIS/Cofins;
and e-book. Performs accounting registration, tax calculation and generation of fiscal books. It has user-level security,
where each registered user is bound to one or more permission types.
With Pegasus, the company will have the facility to manage its business and increase its competitiveness in the market.
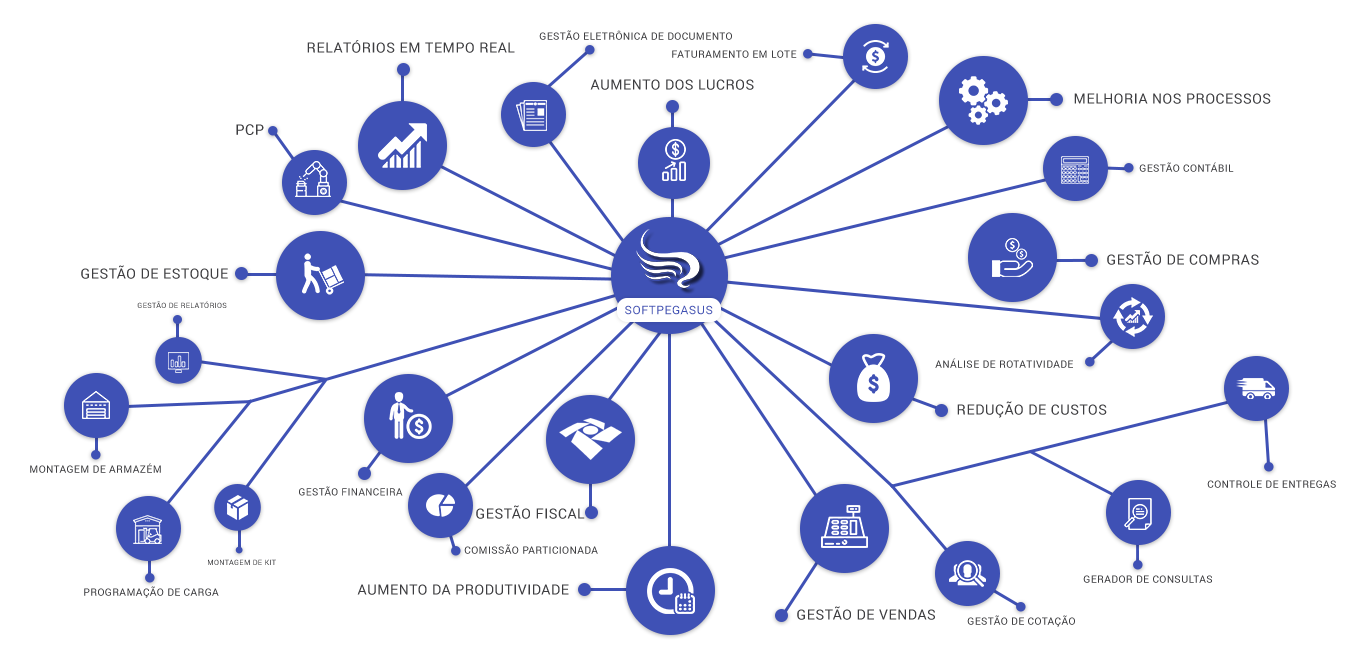
SoftPegasus ERP Features
The constant changes in the market have pushed us to advance in the process capabilities of our software. We use the experiences reported by our partners to develop improvements according to their needs.
- Unified Person Registration;
- Assign multiple addresses to people by address type:
- Thirst;
- Shipping address;
- Billing address.
- Links address to delivery route;
- Links people by type and link group;
- It has an employee record with photo, personal data of the employee, data of the employee in the company, and structured resume;
- Links a supplier to a sales representative;
- It has system access management by permission rules per user group per branch.
- Controls credit policy:
- It has a registration area for socioeconomic registration;
- Records bank and commercial references;
- Levels and classifies client for commercial purpose;
- Links the client to a financial officer;
- Records and controls credit limit.
- Records and controls trading conditions:
- Links client to a promoter and a sales representative, facilitating commission reporting;
- Controls preferential payment condition and term;
- It allows you to make cash and installment sales;
- Controls maximum average term;
- It allows you to make sales in cash, check, duplicate, promissory note, credit card and debit card, and you can have more than one type of document in the sale;
- It can manage term by the average term, recording and controlling maximum average term, average term for interest, maximum term of installments, maximum average term for blocking;
- It can generate an increase or discount by the type of payment condition and by delay or advance of installment;
- Calculates and generates late fees and interest;
- Calculates net income per sale at the time of sale;
- Calculates and manages sales by net income;
- Generates blocks in the sale by situations.
- Registers and controls Contracts and works:
- Registers and controls contracts by advance or by validity;
- Links the advances to the contract, preventing the use of the same in an order not linked to the contract; Links the advances to the contract, preventing the use of the same in an order not linked to the contract;
- Manages the term of the contract;
- Manages the physical and financial balance of the contract;
- Manages monthly invoicing.
- Other Business Processes:
- Follow-up of customer prospecting;
- Spare parts management;
- Sale of processed sheet metal (sells sheet metal and delivers cut parts) integrated with the optway;
- Future sale, triangular sale, order sale, barter;
- Pricing:
- Records purchase price, freight, date and quantity of the last purchase made;
- Registers several ways to calculate COGS through formulas, based on input taxes and constants such as acquisition price, acquisition ICMS, freight, IPI, PIS and purchase charges;
- Records the highest COGS, the lowest COGS, the weighted COGS, and the COGS calculated based on the purchase price of the main supplier;
- It allows you to update or not the COGS from the products input invoice, at this time the system weights the COGS and updates the fields higher COGS, lower COGS, weighted COGS and COGS of the main suppliers table, being able to automatically update prices;
- Allows you to choose which COGS to use, for sales price purposes, among the highest COGS, lowest COGS, weighted COGS or COGS from the main suppliers table;
- Registers several ways to calculate price by means of formulas, based on the Gross Profit that is to be achieved, generating factors by exit taxation (sale), to be applied to the COGS, thus generating the sales price;
- Allows you to work with typed price;
- Records and calculates transfer pricing;
- Allows batch updating of material master data, including price, COGS groups, and price groups;
- Allows you to create multiple standard discount tables to associate with a customer group;
- Allows you to create individual discount tables linked to the customers registration;
- Discount tables have 5 chained discount levels;
- Allows you to give a discount by material group or by material, and the discount given to the material overlaps with the discount given to your group;
- Allows you to update the level 2 group discount, reducing the bulk update work.
- Single registration of materials by company;
- It groups materials by type of sped material (goods for resale, raw material, packaging, product in process, finished product, by-product, intermediate product, material for use and consumption, fixed assets, services, other inputs and others);
- Groups material by expense type and cost;
- Groups material by brand, model, and application;
- It typifies material by industrialized material, resale material, material for use and consumption and industrialized material ready delivery by branch, and one material may have one typification at the head office and another at the branch, or different typifications between the branches;
- Registers manufacturing tree of industrialized material (aggregate material) containing consumption of each input in industrialization, minimum net result, and price factor to be considered in industrialization;
- Registers possible packaging for the materials by registering conversion factor, in relation to the main packaging, net weight, gross weight, area, volume, length;
- It has, in the packaging register, a set of fields for specific control of the glass industry, such as: multiple value in mm; sell only in multiples; inform measurements, to identify that this product, when placed in the sale, opens the glass project; and VPE Glass Project (Glass Ready for Delivery) to link a finished project and this project is automatically forwarded to production when inserted in motion (sale, production order);
- Controls the inventory of materials by batch, varying the only plate registration by plate size in the batch;
- Types the batches to segregate scrap, retail, sale batch, third-party batch, production batch, use and consumption material.
- Inventory Control:
- It has configurable inventory control, allowing you to move inventory according to the companys internal process flow;
- Allows you to move inventory in the inventory, reservation, and order fields;
- It allows you to move stock of materials such as resale, industrialized, industrialized, prompt delivery, use and consumption, scrap, retail and service;
- Moves stock of finished material, its raw material, material in process, scrap and retail according to the companys flow;
- Increases raw material inventory and resale at material receipt (purchase, shipments, transfer, return, other inputs);
- Increases inventory of finished material in the production and return of finished material;
- Increases stock of material in process, scrap and retail in the optimization record when sending the cutting plan to production;
- Increases scrap and retail in the processes of material breakdown in production and retail control;
- Decreases raw material in the optimization record when sending the cutting plan to production;
- Decreases raw material, resale material and scrap at the output of the material (sale, disposal, shipments, transfer, other outputs);
- Decreases material in preparation at the production point or when the material breaks in production, in the retail process;
- Decreases retail in the optimization and output of scrap (sale, disposal, shipments, transfer, other outputs);
- Decreases scrap at the exit (sale, disposal, shipments, transfer, other outputs);
- Decrees finished material at issue (sale, disposal, shipments, transfer, other outputs);
- Decrements finished material in breakage, in shipping processes and retail control;
- Controls minimum stock, days in stock, maximum stock, location and stock per lot;
- Groups batch by date and moves batch without stock;
- Calculates and records ABC curve of products;
- Maintains history, per batch, of the movement of material in the form of kardex tokens;
- Controls physical, financial (COGS) and accounting inventory;
- It has a blind conference process and controls the entry of materials by glue (stack);
- It has process of controlling plate movement, plate entry, sending to easel, sending to cutting, sending to shipping, breaking;
- It has fast inventory counting process by data collector;
- It has an inventory process and adjustment of physical stock and location;
- It has a management process for breaking material in process, and retail management.
- Shopping:
- Allows authorized users to request the purchase of material;
- Allows you to sell material without stock by managing orders;
- It has material turnover management with a process of calculating the replacement of parts, by days of stock coverage, being able to calculate the coverage in the standard unit of measurement or by glue;
- It has a purchase request management that manages requests from orders from authorized users, turnover and order management;
- It has a bidding and budget process, linked to the management of requests, with the generation of quotations;
- It has a purchase authorization process by authority;
- Allows you to enter the nfe xml.
- Warehouse:
- It has simplified material registration for use and consumption material;
- Links the materials of use and consumption to accounting accounts of expenses and costs;
- Breaks down and forwards the requests to the places where the materials are located (warehouse or section);
- Segments faulty material into fault batch;
- Purchased material reserve for the requester who generated the acquisition;
- Low reserve and stock of material when delivered to the requester.
- Registration of Taxes:
- Taxation register linked to tax operation (CFOP), origin, destination and application;
- It is capable of configuring taxation for any tax situations of the Brazilian legislation, including reduction of the calculation basis, tax substitutions by VAT or tariff, special regimes, withholdings, import and export, for companies of real, presumed, simple national profit or individual personnel;
- It applies taxation to tax operations without the interference or need for editing by the operator.
- Tax Operations:
- Configures workflow for sequencing tax operations;
- Locates the pertinent taxation of each item in the operation, applying it to calculate the taxes related to the item in the operation;
- Keeps a record of taxation applied to each item of the operation with its due payments;
- Calculates the taxes of the notes based on the taxation of the items and makes the accounting record, by taxes to be collected, referring to the Nfe issued;
- Generates Nfe according to the authorization of the revenue by sending xml by email of the financial responsible and printing of Danfe;
- Generates receivables and payables in the financial department based on the payment condition and date of issuance of the invoice;
- Generates withholdings and financial documents regarding the amount payable to suppliers and revenue;
- Generates extracts (printouts) of tax operations;
- It manages invoices for the company, allowing you to express awareness of the operation, confirmation of the operation, non-recognition of the operation or operation not carried out, as well as search and view the complete invoice and generate a tax operation related to the entry invoice using the data of the same;
- It executes any type of fiscal operation, such as:
- Issuance of tax coupon;
- Sale of goods and products
- Sale of services;
- Sale of industrialization made by another company;
- Sell order;
- Sale with future delivery;
- Sale of fixed assets;
- Transfer of goods;
- Transfer of fixed assets;
- Complement of taxes;
- Shipment by sales;
- Return of purchases;
- Simple shipping;
- Return of goods;
- Entries by acquisition;
- Receipt of goods for industrialization;
- Entries per consignment;
- Returns to the hospital;
- Sales returns;
- Acquisition of material for use and consumption;
- Acquisition of expenses;
- Acquisition of third-party services.
- Ancillary obligations:
- Sped fiscal, sped contributions, sped accounting;
- E-book;
- DAPI;
- Declan/RJ;
- Gia/PR;
- Gia/RJ;
- Gia/RS;
- Gia/RN;
- Dief PA.
- Findings:
- Calculation of ICMS - Own Operations;
- Calculation of ICMS Tax Substitution;
- Calculation of IPI;
- Pis/Cofins Calculation;
- Documents:
- Generates financial/accounting documents, automatically, from tax operations, linked to your accounting entries, in double sharing;
- It allows you to generate individual documents and budget provisions with their due accounting entries in double sharing;
- The documents have a set of fields for consultation of the entries at interest realized and to be carried out regarding the payment of the same;
- The documents have a history of accounting entries made regarding him/herself, related documents, interest documents and fines;
- The documents have a tab with information on charges and events carried out related to it;
- Documents have specific recordsets per document type:
- Cheque:
- Bank; agency; compensation; cheque nr; type of account; account; and CMC7 code;
- Issuers CNPJ; Issuer; phone; nominal; compensation date; consistency; Return item 1; Return Item 2.
- Fetlock:
- Bank; configuration; 2th copy of the salary; 2th copy value; number; new number; our number; batch shipment; typeable line; barcode, number of prints.
- Duplicate and promissory note:
- Guarantors CNPJ; corporate name of the guarantor.
- Cheque:
- Financial Operations:
- Generates accounts payable, accounts receivable, accruals, collection portfolio from configurable queries;
- Manages payments through payment authorization with authority:
- Accounts payable;
- DARF payable;
- Expenses payable;
- Loans and financing;
- Bank charges;
- Advances to suppliers;
- Payments by cash, check and bank deposit;
- Payments by third-party check;
- Exchange;
- Investments.
- Download documents through document registration, configurable wallet, bank return files or through cash flow tools;
- Manages credit as a result of return of goods or advance payments to suppliers;
- Manages cash or accrual receipts:
- Records unidentified down payments;
- Manages and maintains history of use of advances (checking account);
- Links advance payments from clients to a particular work or order;
- Controls bounced checks, third-party checks, custody checks, as well as slips and receivables checks;
- Calculates, records and controls interest and penalties receivable;
- Records receipts in cash, check, credit card, debit card, duplicate, and promissory note.
- It has a daily bank reconciliation process reflecting the updated bank statement in the system;
- Reconciles credit card;
- Cash and treasury operations:
- It has a cash opening and closing process for several cashiers per sales unit, including truck cashier;
- It has a treasury process;
- Issues synthetic and analytical statement of cash movement;
- Issues bank slips in the banks standard;
- Performs packing list of bank deposit (borderô);
- Makes transfers between bank accounts;
- Write off securities.
- Collection Operations:
- Generates collection portfolio;
- Generates collection portfolio for truck (route collection);
- Records and maintains a history of conversations carried out by the billing operator;
- Records and manages trading.
- Chart of Accounts;
- Organizes the registration of G/L accounts in the form of a chart of accounts;
- It has 4 totalizer account levels and a synthetic account level;
- Registers reference chart of accounts of the revenue;
- Allows you to register several charts of accounts for demonstration purposes;
- Classifies ledger accounts into assets, liabilities, income, and expense;
- Groups G/L accounts for the purpose of financial statements and reports.
- Exercise:
- Closes and opens the fiscal year by promoting the posting of opening balances;
- Controls accounting entries from year and fiscal month, not allowing entries in a closed period;
- Allows you to reconcile accounts from the posting of the accounting document or in the general ledger.
- Accounting Facts:
- Makes journal entry at the time of the accounting fact:
- In the provision and write-off of financial documents;
- In the issuance and release of NFE;
- In the movement of inventory;
- In the request and withdrawal of material in the warehouse;
- In the registration and use of advances to customers and suppliers;
- In cash and banking operations;
- Tax settlements related to special regime and/or tax assessments;
- In the depreciation and valuation of equity.
- Makes journal entry at the time of the accounting fact:
- Patrimony:
- Registers and controls assets, their components and their functions;
- Issues equity position by subsidiary and by business group;
- Links the assets to ledger accounts, for the purpose of posting the accounting facts regarding the life of the asset;
- Links goods to cost center accounts and/or cost center assessment groups to post depreciation to costing;
- They keep a history of the value of the asset from acquisition to its write-off;
- Controls and renews the useful life of the asset;
- It has a depreciation acceleration rate to adjust depreciation of assets that are in heavy use;
- Performs corporate depreciation and tax depreciation;
- Issues CIAP book.
- Costing:
- It has a cost center registration for the appropriation of expenses and costs;
- It has a registration of cost center groups to apportion expenses and costs in more than one cost center;
- Links cost centers to production lines;
- Links cost centers and cost center groups to expense and cost ledger accounts;
- Links cost centers to material groups for settlement;
- Makes the accounting entry and to the cost center automatically or by choice of the operator in business operations;
- Imports personnel expenses from the payroll system, by means of import layout, making the appropriation of expenses and cost in the appropriate cost/expense centers;
- Calculates the monthly cost of each cost center, presenting its result from operational entries, G/L accounts, and material groups;
- Calculates the amount of material produced per period, in m2 or ton, identifying what was appropriated in each cost center;
- Calculates the cost of parts, materials, and material groups by absorbing the cost centers that the parts have passed to be produced;
- It calculates the expenditure of each production cell according to demand, operational and managerial costs.
- It has a register of closing models;
- It has a library of cutouts with the possibility of customizing its features;
- Prepares the design of the project based on basic parameters (width, height, span size);
- It allows you to design and design span closure parts for the application of tempered glass, frame parts, parts for the furniture industry, worked parts, mirrors, laminates, all in scale, containing dimensions of the pieces, cutouts and holes;
- It is integrated into the sales process, generating the parts of the projects in the sale and consolidating the quantity in M2 of the glass to be sold;
- It brings for sale the hardware, kits and aluminum according to the closing model and user parameters;
- Generates printing of the project by piece or complete;
- It integrates the project with the work.
- Planning:
- It allows you to control the entry of daily orders according to production capacity;
- It has laminated sheet production planning process;
- It has a parts manager with a set of filters that allows you to plan the production of cut, tempered, rolled parts, with the most varied built-in services, being able, from predefined parameters, to define parts that go to manual or automatic line;
- It has integration with the Optway optimizer; <
- It has an algorithm that generates optimization of small parts in registered flaps, increasing the use of retail;
- It issues labels, customizable, to monitor the production of the part, with barcode, in the order of the optimized plates and parts.
- Production Control:
- Configures points, physical and logical, for production monitoring;
- Personalizes the monitoring points, based on parameters, according to the characteristics inherent to the workstation;
- Defines production workflow by product group;
- Indicates production by barcode reading on parts and in the parts manager;
- It allows you to point, with a single beep, all the parts of the cutting plane;
- Registers the stack of the sheet used in the cutting plan to maintain the traceability of the plate, supplier and input number of the parts produced;
- Records the batch of parts to maintain traceability of temperate production;
- It allows you to visualize, at the follow-up point, the drawing of the pointed piece in scale, with dimensions and in the color of the glass;
- It has functions, at the follow-up points, to see the part in full screen or in the closing project, to register breakage and to locate the part;
- It has a graphic and dynamic panel informing the number of pieces and in m2 that passed at each monitoring point, visually presenting, from predefined parameters, possible failures in the process;
- It has a problem release process, integrated with the retail management process, to proceed with the parts pointed out with a problem, classifying them as rework, partial loss and total loss;
- Displays the point of the part in the parts manager, in the load schedule, and in the sale;
- It presents in the ecommerce if the piece is in production or if it is already ready.
- Registration of vehicles with tare weight and load capacity;
- Registration of dynamic routes;
- Controls shipment of industrialized material by order, resale and industrialized material for prompt delivery;
- Load schedule including orders in production for a given delivery route;
- It has monitoring of orders and parts in production of a given load;
- Do batch billing by load (route) with a single click;
- Issues loading report;
- Issues packing list grouped by customer (several orders);
- Sends packing list by email at the time of cargo invoicing;
- Tracks cargo;
- Performs delivery control;
- It has a questionnaire for quality control.
- Manages technical calling;
- Allows for cascading tickets;
- Manages attendance;
- Service route program.
- Standard Reports:
- People:
- Title history per person:
- Overdue securities;
- Bonds to Mature;
- Paid Bonds;
- Customer Advances;
- Orders placed.
- Title history per person:
- Materials:
- Kardex;
- Inventory;
- ABC Curve;
- Turnover.
- Production:
- Production map;
- Movement production status;
- Real-Time Production;
- Daily Production;
- Problem Statistic.
- Patrimony:
- Depreciation of Assets (Tax and Corporate).
- Accounting Reports:
- Reason;
- Balance sheet;
- Balance sheet;
- DRE;
- Chart of Accounts;
- Daily.
- Tax Reporting:
- SPED.
- Financial:
- Cash opening;
- Cash Closing;
- Cash flow.
- People:
- Classic Reports:
- People:
- Customer Registration;
- Supplier Registration;
- User Registration;
- Employee Registration.
- Material:
- Materials Group;
- Registration of Materials;
- Pricing Registration;
- Inventory Management;
- Purchases by Material;
- Inventory Counting;
- Bookings by Movement.
- Motion Control:
- Types of Movements Conference;
- Shipment Control for Industrialization and Repair;
- Triangular Operation Control;
- Control of Easels and Necklaces.
- Commercial:
- Partnership Agreement;
- Average Sales Value;
- Sales Orders.
- Financial:
- Financial Operations Conference;
- Customer Analysis;
- Sales/Billing;
- Cash Closing;
- Customer Credits per Period;
- Advance to Suppliers;
- delinquent customers;
- Bounced Checks;
- Advance Receipt;
- Financial Forecasting;
- Recipes;
- Expenditure.
- Billing:
- Packing list by Billing Lot;
- Packing list by indicator;
- Loose Packing List.
- Fiscal:
- Taxation Conference;
- Invoices issued;
- Entry Registration Book;
- Output Registration Book;
- Calculation of ICMS - Own Operations;
- Calculation of ICMS Tax Substitution;
- Calculation of IPI;
- Pis/Cofins Calculation;
- exemption on gross revenue;
- Consolidation of Values by CFOP.
- CIAP Book.
- Production Control:
- Parts Stopped in Production;
- Losses/Problems/Production Status;
- Types: Problems;
- Tags Employees.
- People:
- Electronic Document Management (EDM):
- Saves excel, word, pdf and scanned documents, linked to the asset register, billing, ledger account, contract, documents, employee, material, movements, work, optimization, person, glass project, prospecting and sped;
- Manage and address documents and can be included, viewed, modified and deleted easily and quickly.
- Bulk Registration:
- It has a tool for duplicating registration in the registration of people, materials, taxation;
- It has a tool for updating common records in bulk for the registration of matters and pricing, and can use formulas for updating price and COGS.
- Report Generator:
- It has a tool to develop reports using the SQL language, allowing you to make on-screen reports with parameters passed by the user;
- It has a graphical tool to tabulate and organize for printing the developed reports, and can even use images.
- Query Generator:
- It has a tool to make quick queries and reports, through logical commands and mathematical operators, giving any user of the system the opportunity to develop their queries;
- The graphical print tab tool also works in conjunction with the query generator;
- Questionnaire Generator:
- It has a tool to carry out surveys of employees, customers and suppliers, which can be used linked to any type of movement, such as: purchase; sale; transfer;
- The tool is composed of a register of questions, a response register and the questionnaire register that lists the registration questions that are part of that questionnaire and their possible answers.
- Agenda Generator:
- The System has a tool to generate schedules linked to the status of movements, these schedules generate an alert in the Windows tray.
- Appearance:
- The system has plugins, themes and colors for the user to choose the appearance of the screens most linked to their character, visual comfort or mood.
See what our customers are saying
"Viminas has been a Softsystem customer since 2014. The system allows us to have a complete interaction with the production; thus providing credibility and trust in the services provided."
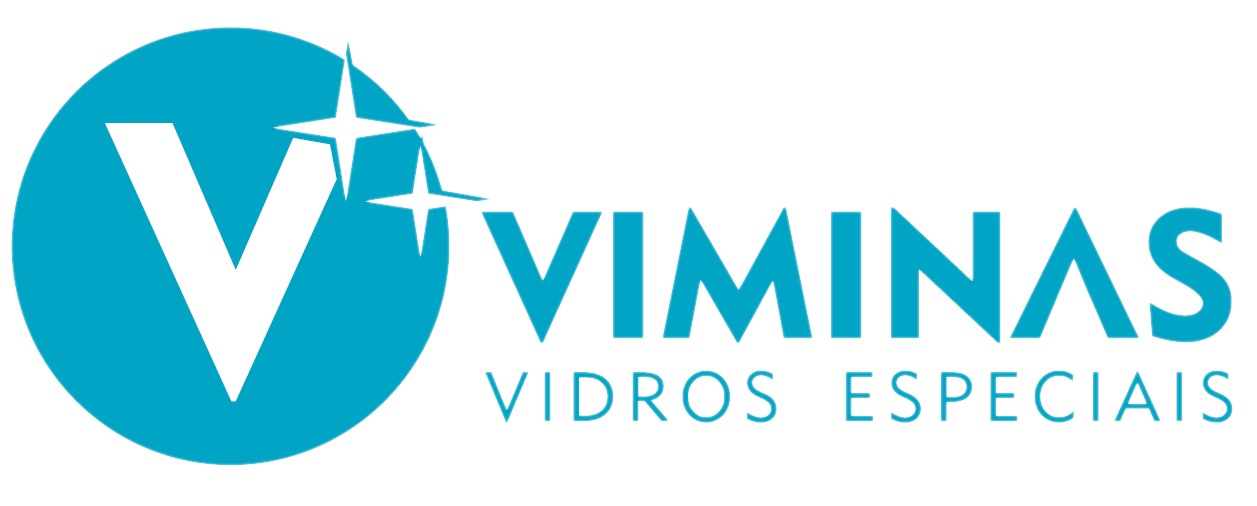
Laura Siqueira - Viminas
"We chose Pegasus because its a system that controls our inventories. In addition, it provides me with real-time production reports. The features that the system brings are essential for the growth of our company."
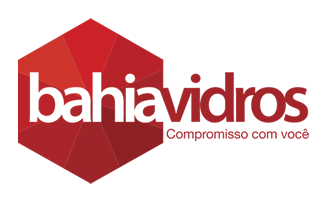
Rogério Ferreira, Bahia Vidros - Three-year partnership with Softsystem
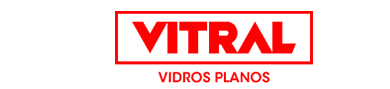
Maurício Chiovato, Vitral - Partner of Softsystem Tecnologia since 2008.